图书介绍
材料成形与失效PDF|Epub|txt|kindle电子书版本网盘下载
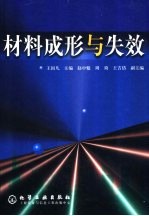
- 王国凡主编 著
- 出版社: 北京:化学工业出版社
- ISBN:7502540121
- 出版时间:2002
- 标注页数:272页
- 文件大小:36MB
- 文件页数:287页
- 主题词:工程材料(学科: 成型) 工程材料(学科: 失效分析) 工程材料 失效分析
PDF下载
下载说明
材料成形与失效PDF格式电子书版下载
下载的文件为RAR压缩包。需要使用解压软件进行解压得到PDF格式图书。建议使用BT下载工具Free Download Manager进行下载,简称FDM(免费,没有广告,支持多平台)。本站资源全部打包为BT种子。所以需要使用专业的BT下载软件进行下载。如BitComet qBittorrent uTorrent等BT下载工具。迅雷目前由于本站不是热门资源。不推荐使用!后期资源热门了。安装了迅雷也可以迅雷进行下载!
(文件页数 要大于 标注页数,上中下等多册电子书除外)
注意:本站所有压缩包均有解压码: 点击下载压缩包解压工具
图书目录
第1章 焊接成形与失效1
1.1 焊接概念与失效分类1
1.1.1 焊接概念1
1.1.2 焊接成形失效分类1
1.1.2.1 焊接裂纹2
1.1.2.2 焊缝中的气孔与夹杂物5
1.1.2.3 焊接结构的变形与应力6
1.2 焊接热裂纹7
1.2.1 结晶裂纹的主要形貌特征7
1.2.1.1 结晶裂纹的形成机理8
1.2.1.2 防止结晶裂纹的措施15
1.2.2 近缝区液化裂纹的主要形貌特征19
1.2.2.1 液化裂纹的形成19
1.2.2.2 液化裂纹与脆性温度区间19
1.2.2.3 影响液化裂纹的因素20
1.2.2.4 防止液化裂纹的措施21
1.2.3 多边化裂纹21
1.2.3.1 多边化裂纹的形成机理22
1.2.3.2 防止措施22
1.3 焊接冷裂纹22
1.3.1 一般特点22
1.3.2.4 横向裂纹23
1.3.2.3 焊根裂纹23
1.3.3 冷裂纹的形成机理23
1.3.2.1 焊道下裂纹23
1.3.2.2 焊趾裂纹23
1.3.2 冷裂纹分类及形貌23
1.3.3.1 氢在开裂中的作用24
1.3.3.2 钢材的淬硬倾向26
1.3.3.3 焊接接头的应力27
1.3.4 冷裂纹敏感性的判据28
1.3.4.1 碳当量(Ceq或CE)与硬度的关系28
1.3.4.2 冷裂敏感指数29
1.3.4.3 临界冷却速度30
1.3.4.4 拘束度与临界拘束度30
1.3.5 防止冷裂的途径32
1.3.5.1 冶金方面33
1.3.5.2 工艺方面33
1.3.6 焊接冷裂纹失效案例34
1.4 再热裂纹36
1.4.1 再热裂纹的形貌特征36
1.4.2 再热裂纹产生的机理37
1.4.2.1 晶内二次硬化理论38
1.4.2.2 晶界脆化理论38
1.4.3 防止再热裂纹的措施39
1.5.1 层状撕裂的特征及形貌41
1.4.4 焊接再热裂纹失效举例41
1.5 层状撕裂41
1.5.2 层状撕裂的分类及形成机理42
1.5.3 影响层状撕裂的因素43
1.5.3.1 夹杂物的影响43
1.5.3.2 氢的影响43
1.5.4 防止层状撕裂的措施44
1.5.4.1 选用抗层状撕裂好的钢材44
1.5.4.2 从工艺和设计上使Z向的拘束应力最小44
1.6 焊缝中的夹杂和气孔44
1.6.1 焊缝中夹杂的分类及形貌44
1.6.1.3 硫化物夹杂45
1.6.2 防止焊缝中夹杂物的措施45
1.6.1.1 氧化物夹杂45
1.6.1.2 氮化物夹杂45
1.6.3 焊缝中气孔的分类及形貌46
1.6.3.1 氢气孔46
1.6.3.2 氮气孔47
1.6.3.3 一氧化碳气孔47
1.6.4 气孔形成的机理47
1.6.4.1 气泡的生核47
1.6.5.1 冶金因素对气孔的影响48
1.6.5 影响生成气孔的因素及控制措施48
1.6.4.3 气泡的上浮48
1.6.4.2 气泡的长大48
1.6.5.2 工艺因素对气孔的影响49
1.7 焊接应力与变形50
1.7.1 焊接应力与变形的产生50
1.7.1.1 长板条不均匀加热时引起的应力与变形50
1.7.1.2 焊接应力与变形的产生原因50
1.7.2 焊接残余应力52
1.7.2.1 纵向应力52
1.7.2.2 横向应力53
1.7.2.4 管板焊接的残余应力分布54
1.7.2.3 厚板中的残余应力54
1.7.3 调节焊接残余应力的措施55
1.7.3.1 设计方面55
1.7.3.2 工艺方面55
1.7.4 焊后消除焊接残余应力的方法56
1.7.4.1 热处理56
1.7.4.2 锤击消除法56
1.7.4.3 振动消除法57
1.8 焊接接头应力腐蚀裂纹及形貌特征57
1.8.1 应力腐蚀裂纹的形貌特征57
1.8.2 产生应力腐蚀裂纹的机理59
1.8.2.1 电化学理论59
1.8.2.3 应力腐蚀裂纹的扩展60
1.8.2.2 机械破裂应力腐蚀机理60
1.8.3 防止应力腐蚀的措施61
1.8.3.1 正确选择钢材61
1.8.3.2 降低残余应力61
1.8.3.3 焊件表面进行防腐处理62
1.8.3.4 采用阴极保护62
1.8.3.5 制定合理的焊接工艺62
1.8.3.6 采用合理的结构和接头设计62
1.8.4 应力腐蚀裂纹引起的失效举例62
1.9.1.2 点蚀64
1.9.1.4 应力腐蚀裂纹64
1.9.1.3 晶间腐蚀64
1.9.1.1 一般腐蚀(均匀腐蚀)64
1.9.1 不锈钢焊接接头腐蚀分类及形貌特征64
1.9 不锈钢焊接接头的腐蚀失效64
1.9.1.5 缝隙腐蚀65
1.9.2 奥氏体钢焊接接头的晶间腐蚀65
1.9.2.1 奥氏体钢焊接接头产生晶间腐蚀的条件65
1.9.2.2 产生晶间腐蚀的原因65
1.9.3 防止晶间腐蚀的措施66
1.9.4 焊接接头的刀蚀66
1.9.4.1 刀状腐蚀的形貌特征66
1.10.1 焊接接头性能达不到要求造成的失效67
1.10 设计不合理造成的失效67
1.9.4.3 刀蚀的防止措施67
1.9.4.2 刀蚀产生的原因67
1.10.2 应力集中造成的失效70
1.10.2.1 应力集中的概念70
1.10.2.2 焊接结构中的应力集中和减小应力集中的措施70
参考文献73
第2章 铸造成形与缺陷74
2.1 铸造成形方法74
2.1.1 重力作用下的铸造成形74
2.1.1.1 砂型铸造74
2.1.1.2 金属型铸造75
2.1.1.3 熔模成形工艺76
2.1.2.2 压力作用下的液态成形77
2.1.2 外力作用下的液态成形77
2.1.2.1 离心力作用下的液态成形77
2.2 铸件缺陷分类79
2.2.1 铸件质量检验79
2.2.2 铸件缺陷的分类80
2.3 铸件的缩孔和缩松85
2.3.1 铸件缩孔、缩松的形貌特征85
2.3.2 铸件缩孔、缩松的形成机理86
2.3.2.1 合金收缩的三个阶段86
2.3.2.2 缩孔的形成机理87
2.3.3 铸件缩孔、缩松产生的原因88
2.3.2.3 缩松形成的机理88
2.3.4 防止铸件产生缩孔、缩松的措施90
2.4 铸造应力、变形及裂纹91
2.4.1 铸造应力的产生原因及特点91
2.4.2 铸件变形产生的原因及防止措施91
2.5 铸造裂纹93
2.5.1 铸造热裂纹93
2.5.1.1 热裂纹的形貌和特征93
2.5.1.2 热裂纹形成的原因93
2.5.1.3 热裂纹的防止措施94
2.5.2.2 冷裂纹形成的原因95
2.5.2.1 冷裂纹的形貌和特征95
2.5.2 铸造冷裂纹95
2.5.2.3 冷裂纹的防止措施96
2.6 铸件气孔97
2.6.1 气孔的形貌特征及种类97
2.6.2 气孔形成的原因98
2.6.2.1 侵入气孔的形成原因98
2.6.2.2 卷入气孔的形成原因100
2.6.2.3 析出气孔的形成机理100
2.6.2.4 反应气孔的形成原因102
2.6.3 防止气孔产生的措施103
2.7.2 铸件夹杂的形貌及产生的原因104
2.7.1 铸件夹杂缺陷的分类104
2.7 铸件夹杂104
2.7.3 防止夹杂类缺陷的措施107
2.8 铸造组织缺陷107
2.8.1 铸造组织缺陷的形貌及产生的原因107
2.8.2 防止铸造组织缺陷的措施108
参考文献108
第3章 塑性成形工艺与失效110
3.1 塑性成形概念与失效分类110
3.1.1 塑性成形概念110
3.1.2 塑性成形失效分类112
3.2 中小型拉深件成形工艺与失效112
3.2.1 拉深变形的特点113
3.2.2 中小型拉深件的主要失效形式115
3.2.3 防止拉深件失效的措施121
3.2.4 中小型拉深件失效举例122
3.3 大型覆盖件成形工艺与失效123
3.3.1 大型覆盖件的成形工艺与特点123
3.3.2 大型覆盖件的失效形式及防止措施126
3.3.2.1 破裂126
3.3.2.2 成形表面形状不良129
3.3.2.3 尺寸精度不合格130
3.3.3 大型覆盖件失效举例130
3.4.2.1 回弹132
3.4.2 变曲成形常见的失效形式及防止措施132
3.4 弯曲成形工艺与失效132
3.4.1 弯曲变形过程132
3.4.2.2 弯曲裂纹133
3.4.2.3 挠曲和扭曲变形134
3.4.2.4 偏移135
3.4.3 变曲成形件失效举例135
3.5 翻边成形工艺与失效136
3.5.1 翻边成形的特点137
3.5.2 翻边成形主要失效形式137
3.5.3 防止翻边成形失效的措施137
3.5.4 翻边成形失效举例138
3.6.1 胀形成形的特点139
3.6 胀形成形工艺与失效139
3.6.2 胀形的失效形式140
3.6.3 防止胀形失效的措施140
3.6.4 胀形失效举例141
3.7 锻造成形与失效142
3.7.1 影响锻件质量的因素142
3.7.2 锻造过程中常见的失效形式与防止措施144
3.7.3 锻造失效形式举例152
3.8 挤压成形与失效154
3.8.1 挤压成形154
3.8.2 挤压成形常见的失效形式与防止措施156
3.8.3 挤压成形失效举例159
参考文献161
第4章 零件铆接、胶接(粘接)工艺与失效162
4.1 零件铆接工艺与失效162
4.1.1 铆接工艺162
4.1.2 铆接失效类型、形成原因及解决办法164
4.1.3 零件铆接失效举例166
4.2 零件胶接工艺与失效167
4.2.1 胶接原理167
4.2.1.1 粘接力的形成167
4.2.1.2 粘接理论168
4.2.2.2 胶接接头设计169
4.2.2 胶接工艺169
4.2.2.1 胶接前处理169
4.2.2.3 胶粘剂的配制与涂敷170
4.2.2.4 胶粘剂的固化170
4.2.3 胶接失效171
4.2.3.1 胶接接头的破坏力学171
4.2.3.2 影响粘接破坏的因素172
4.2.4 常见的粘接失效形式及防止措施172
4.2.5 胶接强度检验175
4.2.5.1 胶接强度检验的一般要求175
4.2.5.3 均匀扯离强度试验176
4.2.5.4 不均匀扯离强度试验176
4.2.5.2 剪切强度试验176
4.2.5.5 剥离强度试验177
4.2.5.6 持久强度试验177
4.2.5.7 疲劳强度试验177
参考文献177
第5章 零件设计及机械加工失效178
5.1 机械零件设计失效类型178
5.1.1 机械零件的失效形式和设计准则178
5.1.2 由载荷引起的零件失效分析180
5.1.3 结构设计不合理造成的失效186
5.2.1 金属切削加工表面质量对零件使用性能的影响191
5.2 金属零件切削加工缺陷与失效191
5.2.2 零件已加工表面的缺陷及原因192
5.2.3 提高零件加工表面质量的措施193
5.3 金属零件的磨削加工缺陷与失效196
5.3.1 金属零件磨削加工缺陷的种类196
5.3.2 提高零件磨削加工表面质量的措施198
参考文献199
第6章 金属脆性断裂与疲劳失效200
6.1 金属脆性断裂200
6.1.1 断裂的类型200
6.1.2 脆性断裂失效现象及特征201
6.1.2.1 脆性断裂失效现象201
6.1.2.2 脆性断口宏观形貌特征203
6.1.2.3 脆性断口微观形貌特征204
6.1.3 脆性断裂的裂纹萌生与扩展206
6.1.3.1 脆性裂纹的萌生机理206
6.1.3.2 脆性裂纹的扩展209
6.1.4 脆性断裂失效原因分析209
6.1.4.1 应力分布209
6.1.4.2 温度210
6.1.4.3 尺寸效应210
6.1.4.4 焊接质量210
6.1.4.5 环境210
6.1.4.6 材料化学成分与组织211
6.1.5.2 调整化学成分212
6.1.5 防止脆性断裂失效的途径212
6.1.5.1 材料的设计与制造212
6.1.5.3 细化晶粒213
6.1.5.4 形变热处理213
6.1.5.5 亚温淬火213
6.1.5.6 低碳马氏体强化213
6.2 金属的疲劳失效214
6.2.1 疲劳断裂现象及特征214
6.2.1.1 疲劳断口的宏观形貌特征215
6.2.1.2 疲劳断口的微观形貌特征218
6.2.2.1 零件加工后疲劳裂纹实际状态的萌生方式219
6.2.2 疲劳裂纹的萌生机理219
6.2.2.2 表面不存在应力集中疲劳裂纹的萌生方式220
6.2.3 疲劳裂纹的扩展222
6.2.3.1 疲劳裂纹扩展的宏观规律222
6.2.3.2 疲劳裂纹扩展的微观机理224
6.2.4 疲劳失效原因分析226
6.2.4.1 表面状态226
6.2.4.2 零件的几何形状及尺寸226
6.2.4.3 装配与连接效应226
6.2.4.4 载荷特性226
6.2.4.5 材料的组织和性能226
6.2.5.1 降低作用于零件危险部位上的实际应力227
6.2.5.2 采用滚压或喷丸使表面强化227
6.2.4.6 使用环境227
6.2.5 防止疲劳失效的措施227
6.2.5.3 表面进行热处理228
6.2.5.4 复合强化228
6.2.5.5 减少夹杂物228
6.2.5.6 细化晶粒228
6.2.5.7 其他因素228
参考文献228
7.1.1.1 过量变形失效230
7.1.1 失效与失效类型230
7.1 失效概述230
第7章 失效分析步骤与检验方法230
7.1.1.2 断裂失效231
7.1.1.3 表面损伤失效231
7.1.2 失效的过程性分析231
7.1.3 失效分析的程序及步骤232
7.2 金属断裂失效分析232
7.2.1 现场调查232
7.2.1.1 现场调查的内容232
7.2.1.2 现场调查的方法232
7.2.2 残骸分析233
7.2.1.3 现场调查的背景资料与注意事项233
7.2.3 实验研究234
7.2.3.1 宏观检验234
7.2.3.2 微观检验235
7.2.3.3 金相检验235
7.2.3.4 无损检验235
7.2.3.5 化学成分分析236
7.2.3.6 力学性能测定236
7.2.3.7 断裂力学分析237
7.2.4 综合分析237
7.3.1 金属断口的基本类型238
7.3.2 允许缺陷断口和报废缺陷断口的基本特征238
7.3 断口分析238
7.3.3 宏观断口分析240
7.3.3.1 实际构件断口的宏观特征241
7.3.3.2 宏观断口分析241
7.3.4 微观断口分析244
7.3.4.1 断口的产物分析244
7.3.4.2 断口的微观形貌分析244
7.3.5 塑性断口特征244
7.3.5.1 静载荷下的断口宏观特征245
7.3.5.2 冲击断口的宏观形貌246
7.3.5.3 韧性断裂的断口微观特征247
7.4 断口试样的选择、清洗及保存248
7.4.1 断口试样的选择248
7.4.1.1 主断面(主裂纹)的宏观判断248
7.4.1.2 断口试样的截取249
7.4.2 断口试样的清洗250
7.4.2.1 清洗前的检查250
7.4.2.2 断口的清洗250
7.4.3 断口试样的保存251
7.5 金相分析252
7.5.1 失效部位试样的选取252
7.5.2.2 机械嵌镶法253
7.5.2.1 塑料嵌镶法253
7.5.2 试样大小及镶嵌253
7.5.3 试样磨制及抛光254
7.5.3.1 试样磨制254
7.5.3.2 试样的抛光256
7.5.4 试样的浸蚀256
7.5.4.1 化学浸蚀剂257
7.5.4.2 化学浸蚀操作257
7.5.5 试样的电解抛光及电解浸蚀258
7.5.5.1 试样的电解抛光258
7.5.5.2 试样的电解浸蚀259
7.6 化学分析259
7.6.1.1 光谱分析260
7.6.1 母材化学成分分析260
7.6.1.2 常规湿法化学成分分析262
7.6.2 微区化学成分分析263
7.6.2.1 电子探针分析263
7.6.2.2 离子探针分析264
7.6.2.3 俄歇电子能谱分析(AES)265
7.6.3 力学性能分析266
7.6.3.1 硬度试验266
7.6.3.2 拉伸试验267
7.6.3.3 冲击试验270
参考文献271