图书介绍
模具制造PDF|Epub|txt|kindle电子书版本网盘下载
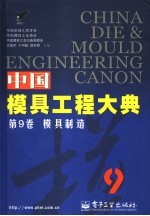
- 王敏杰,于同敏,郭东明主编 著
- 出版社: 北京:电子工业出版社
- ISBN:7121045303
- 出版时间:2007
- 标注页数:1494页
- 文件大小:133MB
- 文件页数:1520页
- 主题词:模具-制造
PDF下载
下载说明
模具制造PDF格式电子书版下载
下载的文件为RAR压缩包。需要使用解压软件进行解压得到PDF格式图书。建议使用BT下载工具Free Download Manager进行下载,简称FDM(免费,没有广告,支持多平台)。本站资源全部打包为BT种子。所以需要使用专业的BT下载软件进行下载。如BitComet qBittorrent uTorrent等BT下载工具。迅雷目前由于本站不是热门资源。不推荐使用!后期资源热门了。安装了迅雷也可以迅雷进行下载!
(文件页数 要大于 标注页数,上中下等多册电子书除外)
注意:本站所有压缩包均有解压码: 点击下载压缩包解压工具
图书目录
第1篇 模具制造技术基础3
第1章 模具制造基本知识3
1 尺寸公差与圆柱体结合的精度设计3
1.1 机械精度设计概述3
1.2 标准公差4
1.3 基本偏差6
1.4 公差带与配合代号的识别19
1.5 圆柱体结合的精度设计(含滚动轴承结合的精度设计)21
2 形状、位置公差32
2.1 概述32
2.2 形状公差和轮廓度公差的标注与公差带33
2.3 定向公差的标注与公差带56
2.4 定位公差的标注与公差带59
2.5 跳动公差的标注与公差带63
2.6 形位公差与尺寸公差的关系65
2.7 形位误差的检测方案73
2.8 形状和位置公差的选用75
3 表面粗糙度82
3.1 表面粗糙度的评定82
3.2 表面粗糙度参数及其允许值的确定84
3.3 表面粗糙度的标注方法87
3.4 表面粗糙度的检测88
4 复杂尺寸联系的精度设计89
4.1 基本概念89
4.2 极值法解尺寸链的基计算90
4.3 极值法解零件尺寸链91
4.4 极值法解装配尺寸链94
4.5 大数互换法解尺寸链99
第2章 模具加工精度与表面质量102
1 概述102
2 模具加工精度102
2.1 模具成型件的尺寸精度102
2.2 冲模加工精度102
2.3 塑料注射模加工精度105
2.4 压铸模加工精度106
2.5 其他类模具制造精度108
3 保证加工精度的方法108
3.1 获得尺寸精度的方法108
3.2 获得形状精度的方法108
3.3 获得位置精度的方法108
4 机械加工工艺系统的原始误差108
5 工艺系统的原始误差分析与控制108
6 提高加工精度的途径110
7 加工误差的综合分析110
7.1 概述110
7.2 加工误差的统计分析法110
7.3 加工误差的点图分析法110
7.4 加工误差的分析计算法111
8 机械加工表面质量111
8.1 概述111
8.2 影响机械加工表面粗糙度的主要因素111
8.3 影响机械加工表面物理力学性能的主要因素112
9 切削加工的表面粗糙度113
10 磨削加工表面的粗糙度114
第3章 模具制造工艺规程115
1 模具生产类型与特点115
2 工艺过程和工艺规程116
3 模具零件毛坯和加工总余量122
3.1 毛坯的种类与特点122
3.2 毛坯余量124
4 工艺基准的选择128
4.1 基准的概念128
4.2 工艺基准的选择129
5 模具零件各表面的加工方法和加工顺序130
5.1 模具零件的分析130
5.2 模具零件的各表面的加工方法和路线(步骤)130
5.3 确定工序内容与加工顺序136
6 工序加工余量和工序尺寸138
6.1 工序加工余量138
6.2 工序尺寸及公差的计算148
7 机床的选择150
7.1 选择机床的原则150
7.2 机床的工作精度150
8 模具成型件精加工中切削用量的选择164
9 模具零件加工工艺实例164
第4章 机床夹具设计168
1 机床夹具的功能和应满足的要求168
1.1 机床夹具的功能168
1.2 机床夹具应满足的要求168
2 机床夹具的类型和组成168
2.1 机床夹具的类型168
2.2 机床夹具的基本组成168
3 机床夹具定位机构的设计170
3.1 工件的定位170
3.2 典型的定位方式、定位元件及装置175
3.3 定位误差的分析与计算186
4 机床夹具夹紧机构的设计188
4.1 夹紧机构设计应满足的要求188
4.2 夹紧力的确定188
4.3 常用夹紧机构190
4.4 其他夹紧机构193
5 机床夹的分度和对定194
5.1 分度装置194
5.2 对定装置195
6 可调整夹具的设计196
6.1 可调整夹具的特点196
6.2 可调整夹具的调整方式196
6.3 可调整夹具的设计197
6.4 成组夹具设计198
7 组合夹具设计199
8 模具制造中常用夹具200
参考文献228
第2篇 模具常规切削加工231
第1章 车削加工231
1 车床231
1.1 机床的用途和加工精度231
1.2 机床的运动231
1.3 机床的总布局231
1.4 机床的主要技术参数232
2 车刀232
2.1 车刀的类型和用途232
2.2 硬质合金焊接式车刀234
2.3 机夹重磨式硬质合金车刀236
2.4 机夹可转位车刀237
3 车削加工方法244
3.1 车外圆245
3.2 车孔247
3.3 切断与切槽250
3.4 车圆锥面250
3.5 车螺纹253
3.6 车成形面258
3.7 模具零件的车削加工259
第2章 铣削加工261
1 铣床及铣削加工特点261
1.1 铣床261
1.2 铣削加工特点262
2 铣刀262
2.1 铣刀的分类262
2.2 铣刀几何参数特点263
2.3 铣刀常用规格266
3 铣削用量278
4 分度头282
4.1 分度头的结构与计算282
4.2 单式分度282
4.3 差动分度282
5 铣削加工285
5.1 铣平面285
5.2 铣正多边形285
5.3 铣键槽287
5.4 铣球面288
5.5 铣螺旋槽289
5.6 铣齿式离合器290
5.7 铣齿轮291
5.8 铣凸轮292
第3章 钻、扩、铰、镗削加工294
1 钻削294
1.1 钻床294
1.2 钻头295
1.3 钻孔的方法和注意事项301
1.4 钻削用量302
1.5 提高钻孔质量的措施307
2 扩削309
2.1 扩孔刀309
2.2 扩孔的切削用量311
2.3 提高扩孔钻扩孔质量311
3 铰削316
3.1 铰刀316
3.2 铰刀的合理使用321
3.3 铰削用量322
3.4 提高铰孔加工的质量326
4 镗削331
4.1 镗床331
4.2 镗刀334
4.3 在镗床上镗孔的基本方法344
4.4 镗削用量的选择345
4.5 镗孔时的故障与提高精度措施346
第4章 刨削加工349
1 设备特点349
2 刀具349
2.1 刨刀的种类和用途349
2.2 刨刀的设计要求349
2.3 精刨刀349
2.4 重型刨刀349
2.5 刨刀的刀具角度354
2.6 对刨刀的要求354
3 切削用量355
4 加工质量356
4.1 加工精度356
4.2 精刨表面常见缺陷及消除措施356
第5章 磨削加工358
1 磨削加工设备及特点358
2 磨料与磨具359
2.1 磨料359
2.2 磨具360
3 磨削参数选择及余量的确定362
4 砂轮修整方法和工具的选择364
4.1 普通磨料砂轮的修整与工具364
4.2 超硬磨料砂轮的修整365
5 平面磨削367
6 外圆磨削368
6.1 在中心磨床上磨削工件外圆368
6.2 在无心磨上磨削工件外圆368
7 内圆磨削369
8 坐标磨削369
9 成型磨削369
10 光学曲线磨削370
11 低粗糙度、高精度磨削370
12 高效、强力磨削370
13 常见磨削加工缺陷、产生原因及防止措施372
参考文献375
第3篇 模具特种加工379
第1章 电火花加工379
1 电火花加工的机理与特点379
1.1 电火花加工的机理379
1.2 电火花加工的特点379
2 电火花加工工艺方法分类379
3 电火花加工中的基本工艺规律380
3.1 影响放电蚀除量的主要因素380
3.2 影响加工速度的主要因素382
3.3 影响工具电极损耗的主要因素383
3.4 影响加工表面质量的主要因素384
3.5 影响加工精度的主要因素385
4 电火花加工设备386
4.1 机床的组成及其各部分的功能386
4.2 机床规格、型号和性能388
5 工具电极389
5.1 电极材料的选用389
5.2 电极的设计390
5.3 电极的制造391
6 加工工艺391
6.1 加工工艺流程391
6.2 电火花加工方法391
7 电火花穿孔392
7.1 工具电极392
7.2 穿孔电火花加工方法393
7.3 穿孔电火花加工的工艺过程393
8 电火花强化394
8.1 表面强化层的特性394
8.2 电火花强化工艺395
9 电火花磨削395
10 模具型腔电火花加工396
10.1 工具电极397
10.2 工作液397
10.3 加工工艺397
第2章 电火花线切割加工技术398
1 线切割加工原理与特点398
1.1 加工原理398
1.2 加工特点398
1.3 线切割加工的应用范围399
2 线切割加工机床399
2.1 类型及规格399
2.2 机床组成400
2.3 影响电火花线切割加工效果的工艺指标401
2.4 电火花线切割机床的程序编制404
第3章 电化学加工417
1 电化学加式概述417
1.1 电化学加工分类417
1.2 电化学加工基本理论417
1.3 电解液421
2 电解加工425
2.1 电解加工成型规律425
2.2 电解加工参数对加工结果的影响426
2.3 电解加工设备429
2.4 电解加工技术在模具加工中的应用433
2.5 模具电解加工的其它方法438
3 电解磨削439
3.1 电解磨削加工原理439
3.2 电解磨削工艺和设备440
3.3 电解磨削典型应用444
4 电解修模抛光444
4.1 电解修模抛光基本原理444
4.2 电解机械修模抛光特点445
第4章 超声加工446
1 超声加工的基本原理与特点446
1.1 超声加工的基本原理446
1.2 超声加工的特点446
2 超声加工的设备组成447
2.1 超声波发生器447
2.2 超声振动系统447
2.3 超声加工机床本体449
2.4 磨料悬浮液循环与冷却系统449
3 超声加工的基本工艺规律450
3.1 影响加工速度的主要因素450
3.2 影响加工精度的主要因素451
3.3 影响表面质量的主要因素451
3.4 工具磨损451
第5章 高能束流加工453
1 激光加工453
1.1 激光加工的原理及特点453
1.2 激光加工的基本设备460
1.3 激光加工工艺及模具中的应用466
2 电子束加工478
2.1 电子束加工原理和特点478
2.2 电子束加工装置479
2.3 电子束加工的应用480
3 离子束加工485
3.1 离子束加工的原理、分类和特点485
3.2 离子束加工装置486
3.3 离子束加工应用487
参考文献493
第4篇 模具数控加工497
第1章 数控加工基础497
1 数控机床的基本概念497
1.1 数控机床的定义497
1.2 数控机床的加工原理497
2 数控机床的组成497
2.1 数控系统497
2.2 伺服系统498
2.3 反馈部件498
2.4 机床本体498
3 数控机床的分类498
3.1 按照加工方式分类498
3.2 按照控制运动的方式分类498
3.3 按伺服系统的类型分类498
4 数控机床的坐标定义499
第2章 数控加工程序的编制501
1 数控编程的基本概念501
1.1 数控编程的内容和基本步骤501
1.2 数控编程的方法501
2 数控编程中的G代码标准502
2.1 G指令503
2.2 M指令505
3 G指令手工编程举例507
3.1 车床加工507
3.2 铣床加工508
4 走刀方式509
5 数控加工刀具轨迹生成技术509
5.1 等参数线轨迹加工方法509
5.2 截平面法510
5.3 等残留高度法510
5.4 空间填充曲线法510
5.5 等距偏置法510
6 路径间距的计算511
7 等弦高差法512
8 后置处理512
9 NURBS曲线插补简介513
9.1 NURBS曲线插补的特点513
9.2 NURBS曲线插补算法514
第3章 UG环境下的数控加工程序编制516
1 绘制模型516
1.1 绘制基座516
1.2 绘制凸模形体517
2 凸模仿真加工519
2.1 加工工艺分析519
2.2 预备操作519
2.3 规划分型面、凸模侧壁粗加工刀具路线522
2.4 规划分型面精加工道具路线524
2.5 规划凸模顶面粗、精加工道具路线524
2.6 规划凸模侧面精加工道具路线526
2.7 规划凸模倒角加工路线527
第4章 MasterCAM环境下的数控加工程序编制528
1 加工零件和工艺分析528
1.1 零件分析528
1.2 工艺分析528
2 挖槽粗加工529
2.1 打开CAD模型529
2.2 完善CAD模型529
2.3 选择曲面挖槽粗加工功能529
2.4 选择加工曲面531
2.5 创建加工刀具531
2.6 设置刀具参数531
2.7 设置曲面加工参数531
2.8 拾取限制边界532
2.9 设置挖槽粗加工参数533
2.10 生成刀具路径533
3 等高外形进行花瓣状盒盖型芯侧面精加工534
3.1 隐藏刀具路径534
3.2 选择曲面等高精加工模组534
3.3 选取加工曲面534
3.4 设置刀具参数534
3.5 设置曲面加工参数534
3.6 设置等高外形粗加工参数534
3.7 生成刀具路径534
3.8 检视刀具路径537
4 挖槽加工花瓣状盒盖型芯分型面精加工537
4.1 隐藏刀具路径537
4.2 选择曲面等高精加工模组537
4.3 选取加工曲面537
4.4 设置刀具参数537
4.5 设置曲面加工参数537
4.6 设置挖槽粗加工参数537
4.7 设置切削深度538
4.8 生成刀具路径538
5 平行铣削进行花瓣状盒盖型芯顶面精加工539
5.1 隐藏刀具路径539
5.2 选择曲面平行精加工模组539
5.3 选取加工曲面539
5.4 设置刀具参数540
5.5 设置曲面加工参数540
5.6 设置平行铣削精加工参数540
5.7 生成刀具路径540
5.8 保存文件540
第5章 Cimatron环境下的数控加工程序编制542
1 Cimatron零件设计过程542
1.1 新建零件文件542
1.2 绘制零件草图542
1.3 生成基本拉伸体543
1.4 利用删拉伸生成基本拉伸实体上凹槽543
1.5 利用增加拉伸生成圆台543
1.6 隐藏不必要的实体544
1.7 保存文件544
2 Cimatron数控铣加工的编程545
2.1 加工零件及工艺分析545
2.2 零件加工及相关参数设置546
参考文献557
第5篇 模具表面加工及处理561
第1章 模具表面光整加工561
1 研磨561
1.1 研磨加工机理与分类561
1.2 研具与研磨剂562
1.3 研磨工艺参数569
2 抛光570
2.1 抛光加工机理571
2.2 抛光剂571
2.3 抛光轮573
2.4 抛光工艺参数573
3 挤压珩订磨加工573
3.1 挤压珩磨加工原理574
3.2 挤压珩磨的介质和夹具574
3.3 挤压珩磨的工艺规律575
3.4 挤压珩磨的应用示例576
4 电解抛光577
4.1 影响电解抛光过程的因素577
4.2 电解抛光表面的缺陷及其产生原因578
4.3 钢铁零件的电解抛光579
4.4 铜及其合金的电解抛光581
4.5 铝及其合金的电解抛光582
4.6 复合电解珩磨582
4.7 电解研磨复合抛光583
5 超声加工584
5.1 超声加工的基本工艺规律584
5.2 超声抛光587
6 磁力研磨588
6.1 加工原理及特点588
6.2 磁力研磨加工装置和工艺参数589
6.3 影响磁力研磨加工效果的因素590
6.4 磁力研磨应用实例590
7 基于机模作化学复合作用原理的抛光技术591
7.1 化学机械抛光591
7.2 机械化学抛光593
第2章 电镀与化学镀594
1 电镀594
1.1 基本原理和影响因素594
1.2 镀层的主要性能及用途595
2 单金属电镀596
2.1 电镀铜596
2.2 电镀镍599
2.3 低温镀铁600
2.4 电镀银601
2.5 电镀铬602
3 特种电镀605
3.1 电刷镀605
3.2 复合电镀607
4 非金属材料电镀608
4.1 非金属电镀工艺过程608
4.2 塑料制品镀前预处理609
4.3 其他非金属材料的预处理610
5 电镀施镀方式与设备610
5.1 挂镀610
5.2 滚镀611
5.3 振动电镀612
6 废液处理与环保613
6.1 电镀废液的来源613
6.2 电镀废液的处理方法614
6.3 镀层性能检测615
7 化学镀618
7.1 化学镀镍619
7.2 化学镀铜620
7.3 化学镀镍622
7.4 化学镀钴622
8 复合化学镀623
8.1 常用复合化学镀镍基镀层的工艺规范623
8.2 耐磨复合镀层NiP/SiC624
8.3 自润滑复合镀层Ni-P/AL2O3624
第3章 表面扩散渗透技术626
1 表面扩散渗透工艺的分类及原理626
1.1 分类626
1.2 表面扩散渗透原理627
2 表面渗碳工艺634
2.1 常用渗碳钢及其预处理634
2.2 气体渗碳640
2.3 固体渗碳工艺645
2.4 渗碳零件常见缺陷与对策646
3 表面渗氮工艺648
3.1 渗氮及多元共渗用钢及其预处理648
3.2 渗氮零件技术要求与检测650
3.3 气体渗氮651
3.4 渗氮零件常见的缺陷与对策654
4 表面氮碳共渗工艺655
4.1 气体氮碳共渗656
4.2 盐浴氮碳共渗656
4.3 固体氮碳共渗658
4.4 实例658
5 表面碳氮共渗工艺659
5.1 碳氮共渗的特点659
5.2 碳氮共渗用钢及其热处理659
5.3 气体碳氮共渗660
5.4 碳氮共渗件常见缺陷及防止措施661
6 渗硼663
6.1 盐浴渗硼663
6.2 固体法渗硼665
6.3 实例666
第4章 热喷涂表面覆层技术667
1 热喷涂的种类、特点和原理667
1.1 热喷涂的种类667
1.2 热喷涂的特点667
1.3 热喷涂的一般原理668
1.4 涂层残余应力669
2 氧-乙炔火焰喷涂与喷熔669
2.1 氧-乙炔火焰丝材喷涂技术669
2.2 氧-乙炔火焰粉末喷涂技术670
2.3 氧-乙炔火焰粉末喷熔技术670
3 电弧喷涂技术670
3.1 基本原理670
3.2 电弧喷涂技术的特点671
3.3 电弧喷涂的设备671
3.4 电弧喷涂材料672
3.5 电弧喷涂工艺673
3.6 电弧喷涂技术的发展方向673
4 等离子弧喷涂674
4.1 等离子弧的产生和特点674
4.2 等离子喷涂原理及特点675
4.3 等离子喷涂设备676
4.4 等离子喷涂用粉末及气体677
4.5 喷涂工艺参数677
5 特种喷涂679
5.1 超音速火焰喷涂679
5.2 超音速等离子喷涂680
5.3 低压等离子喷涂681
5.4 气体爆燃式喷涂681
6 热喷涂技术的应用与涂层设计682
第5章 表面改性技术684
1 激光表面改性684
1.1 激光表面淬火684
1.2 激光表面熔凝688
1.3 激光表面合金化688
2 电子束表面改性689
2.1 电子束表面改性基本原理689
2.2 电子束表面改性设备689
2.3 电子束表面改性工艺691
2.4 电子束表面改性技术的特点694
2.5 应用实例与效果694
3 离子注入694
3.1 离子注入原理695
3.2 离子注入装置695
3.3 离子注入工艺及注入层的性能697
4 气相沉积技术701
4.1 物理气相沉积701
4.2 化学气相沉积708
4.3 物理气相沉积与化学气相沉特点和用途比较712
5 电火花表面强化713
5.1 电火花表面强化的原理714
5.2 电火花表面强化机理714
5.3 电火花表面强化层的特性714
5.4 电火花强化的工艺参数及质量控制715
5.5 电火花表面强化的应用716
参考文献717
第6篇 模具精密与微细加工721
第1章 模具精密和超精密加工技术721
1 精密加工和超精密加工概述721
1.1 精密加工和超精密加工的范畴721
1.2 精密加工和超精密加工的分类721
1.3 影响精密加工和超精密加工的因素725
1.4 精密加工和超精密加工的几个原则728
1.5 精密加工和超精密加工概念的扩展729
2 超精密切削加工730
2.1 超精密切削加工的分类与应用730
2.2 微量切削732
2.3 金刚石刀具超精密车削加工734
2.4 超精密车削加工用金刚石刀具736
2.5 金刚石刀具的磨损742
2.6 精密切削的其他刀具744
2.7 超精密切削的切削用量745
2.8 超精密切削机床747
3 精密超精密磨削加工755
3.1 精密超精密磨削的分类755
3.2 精密超精密磨削在模具制造中的应用756
3.3 精密超精密磨削的磨具756
3.4 精密超精密磨削砂轮的修整775
3.5 普通砂轮精密磨削781
3.6 超硬磨料砂轮精密磨削784
3.7 精密砂带磨削788
3.8 游离磨料精密研磨与抛光801
3.9 超精密磨削802
第2章 模具微细加工技术809
1 微细加工的概念809
2 微细加工方法809
3 微细车削加工809
3.1 微细车削工艺及基本方法809
3.2 微细车削车床及其加工技术812
4 微细铣削加工813
4.1 微细铣削工具814
4.2 微细铣削工艺815
4.3 微细铣削机床及其加工技术818
5 微细钻削加工820
5.1 微细钻削工艺特点820
5.2 微细钻头820
5.3 小孔加工机床821
5.4 微孔加工注意事项822
5.5 微细钻削应用822
6 微细变形加工824
6.1 变形加工的优缺点824
6.2 变形加工用于微细加工技术时的注意事项824
6.3 应用实例825
7 微细磨料加工825
7.1 磨料的种类825
7.2 研磨加工825
7.3 磨削加工826
7.4 抛光827
8 微细磨料喷射加工827
8.1 加工原理与特点827
8.2 基本工艺方法及参数选择828
8.3 磨料喷射加工应用829
9 化学方法的微细加工829
9.1 一般化学刻蚀829
9.2 化学抛光830
9.3 化学镀膜831
10 微细电火花线切割加工技术831
10.1 微细电火花线切割加工的关键技术831
10.2 微细电火花线切割加工技术的应用832
11 微细电火花加工(简称MEDM)832
11.1 概述834
11.2 微细电火花加工的特点和应用834
11.3 微细电火花加工原理834
11.4 微细电火花加工的工具电极制作835
11.5 高精度微进给驱动装置835
11.6 微小能量脉冲电源技术837
11.7 电火花分层铣削中电极损耗837
11.8 应用实例837
12 微细电化学加工技术841
12.1 微细电化学蚀刻加工841
12.2 超短脉冲微细电化学加工843
12.3 微细轴孔的微细电化学加工844
12.4 微细电铸成形845
13 高能束微细加工848
13.1 微细激光加工849
13.2 微细电子束加工864
13.3 微细离子束加工870
14 微细超声加工876
14.1 微细超声加工机理和特点876
14.2 超声加工应用876
15 光刻加工878
15.1 光刻加工基本过程878
15.2 紫外光刻881
15.3 粒子束光刻881
15.4 光刻胶882
15.5 深度光刻技术882
16 LIGA和准LIGA工艺883
16.1 LIGA工艺特点883
16.2 LIGA的基本工艺过程883
16.3 准LIGA技术884
16.4 LIGA和准LIGA微细加工应用886
参考文献892
第7篇 典型模具制造895
第1章 冲压模具制造895
1 冲压模具结构与分类895
2 冲压模具的制造特点896
3 冲压模具的制造过程897
4 冲压模具的加工工艺方法898
5 各类冲模的制造要点898
5.1 冲裁模898
5.2 弯曲模914
5.3 拉深模915
5.4 冷挤压模917
第2章 塑料模具的制造921
1 概述921
2 塑料模具制造技术要求921
3 塑料模具成形零件的制造特点与要求922
4 塑料注塑模具制造922
4.1 注塑模具的结构组成与零件类型923
4.2 注塑模具制造的技术要求924
4.3 注塑模具的制造特点927
5 塑料压塑模与压注模具的制造950
5.1 塑料压塑模具的制造950
5.2 塑料压注模具的制造957
6 塑料吹塑模具的制造工艺要点957
7 塑料挤出模具制造工艺要点962
8 塑料热成形模具制造工艺要点968
第3章 金属压铸模具的制造970
1 概述970
2 压铸模具的典型结构及零件类型970
3 压铸模具的制造特点与技术要求972
3.1 压铸模具的制造特点972
3.2 压铸模具的制造技术要求973
4 压铸模具零件制造975
4.1 分型面加工975
4.2 成形零件制造976
4.3 其他零件加工982
第4章 锻压模具和粉末冶金模具制造986
1 锻压模具的制造986
1.1 概述986
1.2 锻模的技术要求987
1.3 锻压模制造工艺过程994
2 粉末冶金模具的制造995
2.1 粉末冶金模具制造的技术要求995
2.2 模具主要零件的加工工艺流程998
2.3 模具零件的典型加工工艺举例1002
第5章 汽车覆盖件模具制造1005
1 覆盖件模具制造技术特点1005
2 覆盖件模具的生产技术准备1005
3 覆盖件模具的制造工艺流程1008
4 覆盖件拉深的特点1009
5 覆盖件拉深模具的结构1010
6 覆盖件拉深模具的制造步骤1011
7 覆盖件拉深模具的制造1012
8 修边模制造1016
9 覆盖件冲模制造新技术1023
第6章 简易模具的制造1028
1 低熔点合金模具制造1028
1.1 低熔点合金的成分与性能1028
1.2 低熔点合金模具的浇注方法1028
2 锌基合金模具制造1029
2.1 模具用锌基合金的性能1030
2.2 锌合金模具的制造工艺1030
3 陶瓷铸型模具制造1033
3.1 陶瓷型铸造工艺1034
3.2 陶瓷型铸造模具的特点1035
4 聚氨酯橡胶模具制造1035
4.1 聚氨酯材料的特点与性能1035
4.2 聚氨酯铸造模具的制造工艺1036
参考文献1038
第8篇 模具制造质量检测与控制1041
第1章 模具零件的检测1041
1 概述1041
2 长度尺寸测量1041
2.1 轴、孔类零件测量工具1041
2.2 轴类零件的测量1042
2.3 孔类零件的测量1043
3 形状误差的测量1044
3.1 概述1044
3.2 直线度误差的测量1044
3.3 平面度误差的测量1045
3.4 圆度误差的测量1045
3.5 圆柱度误差的测量1046
3.6 轮廓度误差的测量1047
4 位置误差的测量1047
4.1 概述1047
4.2 定向误差的测量1048
4.3 定位误差的测量1048
4.4 跳动误差的测量1049
5 表面粗糙度的测量1050
5.1 概述1050
5.2 表面粗糙度的测量1050
6 角度和锥度的测量1051
6.1 概述1051
6.2 角度和锥度的测量1051
7 尺寸链1053
7.1 概述1053
7.2 尺寸链极值法计算1054
7.3 尺寸链在零件检测中的应用实例1054
8 坐标测量技术与坐标测量机1055
8.1 坐标测量技术的基本概念1055
8.2 坐标测量机的组成1055
8.3 坐标测量机的类型1057
8.4 坐标测量机的测量方式1058
8.5 坐标测量机的应用1059
9 模具零件质量评价1061
9.1 模具零件质量评价内容1061
9.2 模具零件质量评价特点1061
第2章 模具企业质量管理1062
1 质量管理概述1062
1.1 质量管理的概念1062
1.2 质量管理的发展阶段1063
2 质量控制技术1064
2.1 常用统计方法1064
2.2 质量成本控制1069
3 全面质量管理1070
3.1 全面质量管理概述1070
3.2 全面质量管理的内容1071
3.3 全面质量管理的工作方法1072
3.4 模具制造的质量管理1073
4 ISO9000系列标准与认证1074
4.1 质量认证的概念和分类1075
4.2 ISO9000系列标准1075
4.3 质量体系认证的程序1076
第3章 模具计算机辅助质量系统1078
1 计算机辅助质量系统概述1078
1.1 系统产生的背景1078
1.2 系统总体目标及其作用1078
1.3 系统功能结构1079
2 质量规划与决策1081
3 质量数据采集1082
3.1 系统的设计思想及总体结构1082
3.2 系统的主要功能和特点1083
4 质量评价与控制1083
4.1 质量评价组成1083
4.2 质量控制组成1085
4.3 工序质量控制功能结构1085
5 计算机集成质量管理系统1086
5.1 CAQ系统综合集成结构模型1086
5.2 CIMS环境下CAQ系统的信息集成1087
参考文献1089
第9篇 模具装配与试模调整1093
第1章 模具装配技术1093
1 概述1093
1.1 模具装配的概念1093
1.2 模具装配精度及技术要求1093
1.3 模具装配的工作内容1096
2 模具装配的工艺过程与方法1097
2.1 模具装配工艺规程1097
2.2 模具装配的工艺过程1097
2.3 模具的装配方法1098
2.4 装配尺寸链1099
3 模具零件的固定方法1100
3.1 机械固定法1100
3.2 物理固定法1104
3.3 化学固定法1108
第2章 冲压模具的装配1113
1 冲压模具的装配要点及装配顺序选择1113
2 冲压模具的装配1114
3 各类冲压模具的加工与装配过程1118
4 覆盖件拉深模的装配工艺过程1119
5 装配示例1120
5.1 单工序冲裁模的装配1120
5.2 连续模装配1123
5.3 复合模的装配1125
第3章 塑料模具的装配1127
1 注塑模具的装配1127
1.1 注塑模具的装配要点1127
1.2 注射模具的装配内容与方法1128
1.3 注射模具的装配实例1138
2 压塑模具与压注模具的装配1139
2.1 压塑模具及压注模具的装配过程及要点1139
2.2 压塑模具的装配实例1140
2.3 压注模具装配实例1141
3 挤塑模具的装配1142
3.1 挤塑模具的装配要求1142
3.2 挤塑模具的装配过程与要点1142
3.3 装配实例1143
4 中空吹塑模具的装配1143
5 塑料模具装配后的检查1145
第4章 金属压铸模具的装配1146
1 压铸模具的装配特点与要求1146
2 压铸模具的装配实例1146
3 压铸模具装配后的检查1148
第5章 模具的试模、调整与验收1150
1 试模的目的与要求1150
2 塑料模具的试模与调整1150
2.1 注塑模具的试模与调整1150
2.2 压塑模具及压注模具的试模与调整1159
2.3 挤塑模具的试模及注意事项1163
2.4 中空吹塑模具的试模要点1167
3 冲压模具的试模与调整1169
3.1 冲压模具试模调整的目的1169
3.2 冲压模具试模的内容与要求1170
3.3 冲压模具的安装与试冲压1171
3.4 冲裁模具的试模与调整1171
3.5 弯曲模具的试模与调整1174
3.6 拉深模具的试模与调整1176
3.7 覆盖件冲模的试模与调整1179
3.8 精冲模的试模与调整1184
4 压铸模具的试模与调整1185
4.1 金属压铸模具的试模工艺过程1185
4.2 压铸模具的试模调整1187
5 模具的验收1189
5.1 冲压模具的验收1189
5.2 塑料注塑模具的验收1190
5.3 压铸模具的验收1191
参考文献1193
第10篇 模具失效、寿命、使用与维护第1章 模具失效与寿命1197
1 模具失效的基础知识1197
1.1 模具失效的概念1197
1.2 模具寿命1199
2 模具工作条件分析1199
2.1 冷作模具工作条件分析1199
2.2 热作模具工作条件分析1200
2.3 塑料模具工作条件分析1201
3 模具失效形式及机理1201
3.1 磨损失效1202
3.2 断裂失效1203
3.3 塑性变形失效1205
3.4 多种失效因素的综合作用1206
4 模具失效的基本因素1206
4.1 模具结构及零件结构对失效的影响1206
4.2 模具材料对失效的影响1207
4.3 模具毛坯锻造缺陷与预处理对失效的影响1207
4.4 模具冷加工缺陷对失效的影响1207
4.5 模具热处理缺陷对模具失效的影响1209
4.6 模具表面处理缺陷对模具失效的影响1212
4.7 模具装配缺陷对模具失效的影响1214
4.8 模具使用与保养对模具失效的影响1214
5 提高模具寿命的措施1215
5.1 正确设计模具结构及零件1216
5.2 模具材料及热处理1217
5.3 正确实施模具毛坯的锻造与预处理1218
5.4 确保模具的冷加工质量1219
5.5 合理选择制件材料1219
5.6 确保模具的装配质量1220
5.7 正确地使用与保养模具1220
6 模具失效分析实例1221
6.1 冷作模具失效分析—Cr12钢冷冲模具断裂分析1221
6.2 塑料模具失效分析—线圈架塑料压注模失效分析1221
6.3 压铸模具失效分析—H13钢大型压铸模早期开裂失效分析1222
6.4 锻压模具失效分析—热穿孔冲头失效分析1224
第2章 模具的使用与维护1227
1 模具的安装与调整1227
1.1 冲压模具的安装与调整1227
1.2 塑料注射模的安装与调整1228
1.3 压铸模的安装与调整1231
2 模具的使用维护与修理1232
2.1 模具的使用与保管1232
2.2 模具的维护与修理1232
3 模具故障的排除1235
3.1 冲裁模故障及其排除1235
3.2 弯曲模故障及其排除1236
3.3 拉深模的故障及排除1236
3.4 冷挤压模的故障及排除1237
3.5 压铸模的故障及排除1237
3.6 锻模的故障及排除1238
3.7 注塑模的故障及排除1238
3.8 其他塑模的故障及排除1238
参考文献1239
第11篇 模具现代制造技术1243
第1章 模具计算机辅助制造1243
1 计算机辅助制造的基本概念1243
1.1 概述1243
1.2 计算机辅助制造的应用1243
1.3 模具CAD/CAM的发展趋势1244
2 模具CAM系统的支撑环境1245
2.1 计算机硬件环境1245
2.2 计算机软件环境1245
3 模具CAD/CAM系统的功能与工作过程1247
3.1 模具CAD/CAM的功能1247
3.2 模具CAD/CAM系统的工作过程1248
4 模具CAD/CAPP/CAM系统集成1248
4.1 CAD/CAPP/CAM集成的关键技术1249
4.2 模具CAD/CAPP/CAM系统框架1249
4.3 实现模具CAD/CAPP/CAM集成采取的途径1251
5 计算机辅助数控加工1251
5.1 计算机辅助数控加工的内容1251
5.2 计算机辅助数控加工程序的编制1252
5.3 加工程序的传输1254
第2章 模具网络化制造1258
1 网络化制造的概念和内涵1258
1.1 网络化制造的产生背景1258
1.2 网络化制造的概念和定义1259
1.3 网络化制造的技术内容、功能特点和应用层次1261
1.4 开展模具企业网络化制造的意义1263
2 模具行业网络化制造系统1263
2.1 面向模具企业的网络化制造系统1264
2.2 面向模具行业的网络化制造系统1264
2.3 面向区域的模具网络化制造系统1265
2.4 面向动态联盟的网络化制造系统1266
3 网络化制造集成平台1267
3.1 网络化制造集成平台的特点1267
3.2 网络化制造集成平台体系结构1268
4 网络化制造的关键技术1270
4.1 数控资源共享技术1270
4.2 企业应用集成技术1277
5 模具行业网络化制造系统应用案例1280
5.1 西安快速模具制造服务系统概况1280
5.2 深圳模具网络化制造示范概况1283
第3章 模具计算机辅助工艺规划(CAPP)1286
1 CAPP基本知识1286
1.1 CAPP系统的基本结构1286
1.2 CAPP的基本技术1287
2 计算机辅助工序设计1290
2.1 切削用量的确定1290
2.2 工时定额的确定1290
2.3 工序图的自动生成和绘制1291
3 CAPP系统类型结构与实现方法1291
3.1 派生式CAPP系统1291
3.2 创成式CAPP系统1295
3.3 综合式CAPP系统1299
3.4 交互式CAPP系统1300
3.5 智能CAPP系统1301
4 CAPP在模具制造中的应用1304
第4章 模具成组技术(GT)1306
1 概述1306
1.1 成组技术原理1306
1.2 成组技术应用及其技术经济效果1306
2 零件分类与编码和分类系统1307
2.1 分类编码的概念1307
2.2 零件分类编码的作用1314
3 零件分类成组方法1314
3.1 生产流程分析法1315
3.2 编码分类法1316
4 成组工艺和成组生产单元的设计1317
4.1 成组加工工艺1317
4.2 成组生产组织和成组加工单元1318
5 成组技术(GT)在注塑模具中的应用1319
5.1 注塑模具零件的分类1319
5.2 注塑模具零件的编码规则—CCSIM系统1319
第5章 模具高速切削加工1323
1 高速切削加工技术1323
1.1 概述1323
1.2 高速切削加工的机理1326
1.3 高速切削加工机床1327
1.4 高速切削加工刀具1328
1.5 高速切削的数控编程1329
2 模具高速切削加工技术1329
2.1 概述1329
2.2 模具高速切削加工性1331
2.3 模具高速切削加工条件的优化1335
2.4 模具高速切削加工策略1336
2.5 模具高速切削加工应用及实例1337
第6章 快速成形技术与快速制模1347
1 快速成形技术概述1347
1.1 快速成形技术的概念1347
1.2 快速成形技术的工艺过程1349
1.3 快速成形技术常用的文件格式1354
1.4 快速成形材料1355
1.5 RP技术的成形设备1360
1.6 RP技术用于产品的快速制造1362
2 快速模具成形概述1363
2.1 快速模具成形技术的概念1364
2.2 快速模具成形的分类1364
3 硅橡胶模具1366
3.1 硅橡胶模具的材料1366
3.2 硅橡胶模具的制作1367
3.3 硅橡胶模具的特点1367
4 铝填充环氧树脂模1368
5 金属热喷涂模具制造1369
5.1 金属热喷涂模具快速成形技术1369
5.2 电弧喷涂模具制造技术1369
5.3 等离子喷涂制模技术1372
6 选择性激光烧结快速制模1375
6.1 直接金属激光烧结制模1375
6.2 间接金属激光烧结制模1377
6.3 混和金属粉末激光烧结制模1379
7 分层实体制造快速制模1379
7.1 LOM技术在模具制造中的应用1380
7.2 用LOM工艺直接制造木模1380
7.3 利用LOM工艺直接制造金属模具1380
8 粉末浇铸1381
8.1 有黏结剂粉末浇注1381
8.2 无黏结剂干粉浇铸1381
9 层压制模1382
9.1 概述1382
9.2 制造技术1382
9.3 层压成形制造模具需要考虑的几个方面1383
10 光固化成形快速制模1384
10.1 Direct AIM模1384
10.2 SLA成形的树脂壳—铝填充环氧背衬模1385
11 3D Keltool模1386
11.1 3D Keltool模的制作工艺1386
11.2 3D Keltool模的特点1387
12 溶剂熔接自由构建制造模具1387
12.1 溶剂熔接技术简介1387
12.2 溶剂熔接技术工艺1387
13 快速熔模铸造制模1388
14 电铸镍壳—陶瓷背衬模1389
15 快速制模中的低温浸渗处理1390
15.1 浸渗剂1390
15.2 三种常用的浸渗方法1392
15.3 浸渗模型1392
第7章 模具逆向工程1394
1 逆向工程概述1394
1.1 逆向工程的定义1394
1.2 逆向工程的应用范围1394
2 逆向工程的系统构成1395
3 逆向工程的关键技术1396
3.1 数据采集1396
3.2 数据预处理1398
3.3 模型重建技术1404
4 逆向工程在模具设计中的应用1410
4.1 逆向软件简介1410
4.2 逆向工程的应用实例1414
第8章 模具先进制造生产模式1417
1 模具制造并行工程1417
1.1 并行工程的基本概念及特点1417
1.2 模具并行工程的关键技术1419
1.3 模具并行工程的组织模式1423
1.4 模具制造并行工程的集成框架1428
2 模具敏捷制造1430
2.1 敏捷制造的基本概念1430
2.2 模具敏捷制造的技术基础1431
2.3 模具敏捷制造的实施策略1434
2.4 基于CSCW技术的模具设计制造系统及其关键技术1434
2.5 基于多Agent的模具敏捷制造系统和CORBA的应用1437
3 智能制造系统1439
3.1 智能制造的涵义1439
3.2 人工神经网络的模具设计与制造中的应用1440
3.3 汽车覆盖件模具的智能化加工方法1442
参考文献1444
第12篇 模具企业的现代管理1447
第1章 模具企业的生产经营管理1447
1 模具制造的经营管理1447
1.1 模具制造的物资供应管理1447
1.2 模具的订货与销售管理1448
1.3 市场调查与预测1451
1.4 售前售后服务1451
2 模具制造的生产管理1451
2.1 生产计划管理1451
2.2 生产调度工作1452
2.3 生产定额的制定与管理1452
3 模具制造的技术管理1454
3.1 设计者的职责与设计图样的审校1454
3.2 模具加工工艺的制定与编制1455
3.3 技术文件的发放及其管理1457
3.4 模具设计制造总结1457
第2章 模具企业的信息化管理1458
1 企业信息与信息管理概述1458
1.1 信息基本知识1458
1.2 企业信息1460
2 企业信息流与管理信息系统1462
2.1 信息系统的基本概念1462
2.2 企业管理系统的信息流1463
2.3 企业管理信息系统概述1463
3 管理信息系统的生命周期1466
3.1 系统规划1466
3.2 系统分析1468
3.3 系统设计1470
3.4 系统实施1475
3.5 运行与维护1477
4 管理信息系统的实际应用1477
4.1 企业资源计划的原理和应用1477
4.2 产品数据管理原理和应用1486
5 企业信息沟通1491
5.1 企业信息沟通的含义、目的和作用1491
5.2 企业外部沟通1492
5.3 企业内部沟通1492
参考文献1494